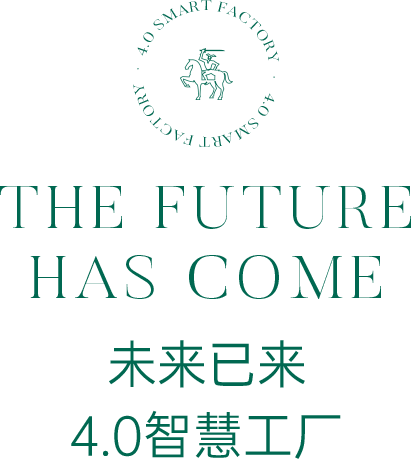
Made in China 2025
In 2017, Copton spent 370 million yuan to build the Industry 4.0 smart factory in accordance with the world's first-class standards.
The smart factory covers an area of 170 mu, including four main parts: tank area, R&D center, comprehensive workshop and automatic storage center. The production capacity can reach 80,000 tons/year of lubricating oil and 20,000 tons/year of antifreeze.
The tank area is divided into five parts: finished additives tank area, basic oil tank area, glycol tank area, integrated plant blending tank area, etc.There are 103 tanks with a total capacity of 29,370 cubic meters.
The comprehensive workshop is composed of sol workshop, production office, laboratory, automatic coordination control office and filling line.The integration of production or production related departments ensures maximum efficiency of production.
There are 19 production lines in the comprehensive plant, including 8 200L VAT filling lines, 4 antifreeze filling lines and 7 lubricating oil filling lines (including 2 OCME production lines). Each production line is connected by an independent pipeline and intersects with the oil pipeline at the universal manifold. The production pipeline at the manifold can be connected with any product pipeline, which greatly saves the time spent on replacing oil products.
The storage center, which adopts three-dimensional storage mode, has 10,560 warehouse locations and can store about 600,000 pieces of various products.
- 170Mu
Total floor area
- 103
Large and small tanks
- 19
Comprehensive plant production lines
- 10560
Automatic warehouse center location
- 600000
Full stock storage products
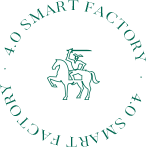
The tank area is divided into five parts: finished additives tank area, basic oil tank area, glycol tank area, integrated plant blending tank area, etc.There are 103 tanks with a total capacity of 29,370 cubic meters.
The total capacity of the raw oil tank area is 4000m³.
The total capacity of the base tank area is 17,000 m³.
The total capacity of additive and refined oil tank area is 5650m³.
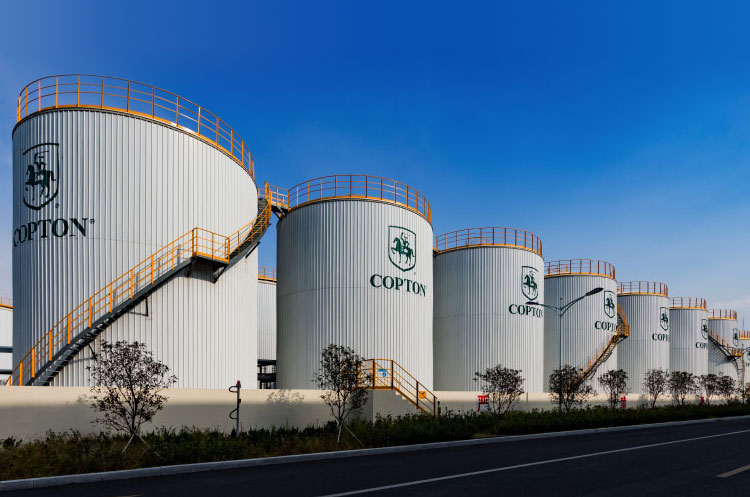
The additive is stored in the special tank line to avoid the mixing in the process of unloading, storage and feeding, which affects the quality of oil.The built-in local heater is installed at the bottom of each tank, and the material is heated step by step during the unloading process to avoid the performance impact caused by repeated heating additives.In addition, there is an electric heat system in each process pipeline to maintain the temperature of the pipeline at the set value, which not only reduces the heat loss during the material conveying process, but also maximizes the blending efficiency.In addition, the storage tanks are equipped with a metering system, which is developed and applied by a global professional metering company. There are not only conventional high-precision liquid level measurement, high and low level alarm, but also real-time report data of each tank liquid level and various reporting systems. It not only meets daily metering accuracy, but also can monitor inventory management in real time.
PIGGING SYSTEM
In the process industries, pigging refers to technology that uses specialist projectiles to recover, rather than waste, residual liquid in pipelines or industrial tubing. Using the pigging system, the residual amount in the pipeline is very low(1g/m).
XP Automatic Ball Manifold
According to the development needs of the project, the management manifold specifications can be expanded in stages. Each inlet and outlet pipe of manifold can be ball-through pipe of different diameter according to production needs. At the same time, one
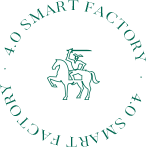
The Emerson global first-class blending system and advanced hardware equipment are adopted to realize the precise SMB synchronous measurement accuracy (0.1%), BBV fast blending (15 ~ 25 min) efficiency, DDU barrelled measurement extraction accuracy (0.1%), the ball pigging, manifold and other blending system integration and metrology management.
Emerson's WINBLEND System Seven is a sophisticated process control system that incorporates Emerson's 40 years of blending expertise and flow metering technology.
For more than 40 years, Emerson has built a wealth of experience as an undisputed industry leader in lubricants.
Advantages:
High degree of automation: The whole blending process is carried out automatically according to the set procedure, without intervention.
Good flexibility: First, the minimum blending quantity of each batch can reach 10~20% of the volume of the blending tank, and large quantities of products can be blended in multiple batches; Second, the process is simplified, the additives can be added quantitatively through DDU, solid additives can be directly poured by manual measurement.
Solved the "hybrid" problem: Blending tank and auxiliary metering tank are made of stainless steel with polished inner wall to reduce oil attachment. Combined with efficient flushing head and self-discharging piping, the tank walls can be cleaned with minimum base oil when switching varieties.Cleansing oil as part of the blending formula into the blending tundish for blending.
Fast production speed: The blending period of a typical batch of 10TABB is 1h.
SMB combines the metering system of pipeline blending (ILB) with the principle of tank blending, which makes the blending flexible.Each part can be added after being measured by the flowmeter, added by manual weighing or added in other different ways.
The advantages of SMB are that it has greater operational flexibility, can switch production of multiple varieties, and has less possibility of cross-contamination,which can meet the needs of a wide variety of products, both large and small batch production.
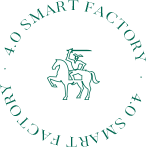
OCME automatic high-speed filler machine is imported from Italy. Each equipment of the whole line is automatically connected by photoelectric sensor equipment to realize high-speed automatic production. OCME automatic high-speed filler machine has its unique integrated system in the design and construction, which has the characteristics of saving space, high single production efficiency, saving labor and so on. In addition, OCME equipment is equipped with intelligent safety protection devices, isolation guardrail and safety door, to ensure the life safety of operators and maintenance personnel to the greatest extent.
The weighing module has passed MID certification, and the quality error can be controlled ≤5‰.
Spray system: There are two spray systems set up in the oil storage box. When switching oil products, the inner wall of the oil tank can be cleaned by the nozzle to avoid residual oil and improve product quality.
Pressure system: The filler machine is equipped with a pressure device. The filling process can be pressurized according to the flow velocity of semi-finished products to improve the filling efficiency. The production speed of 1L specification products can reach 12,000 bottles per hour.
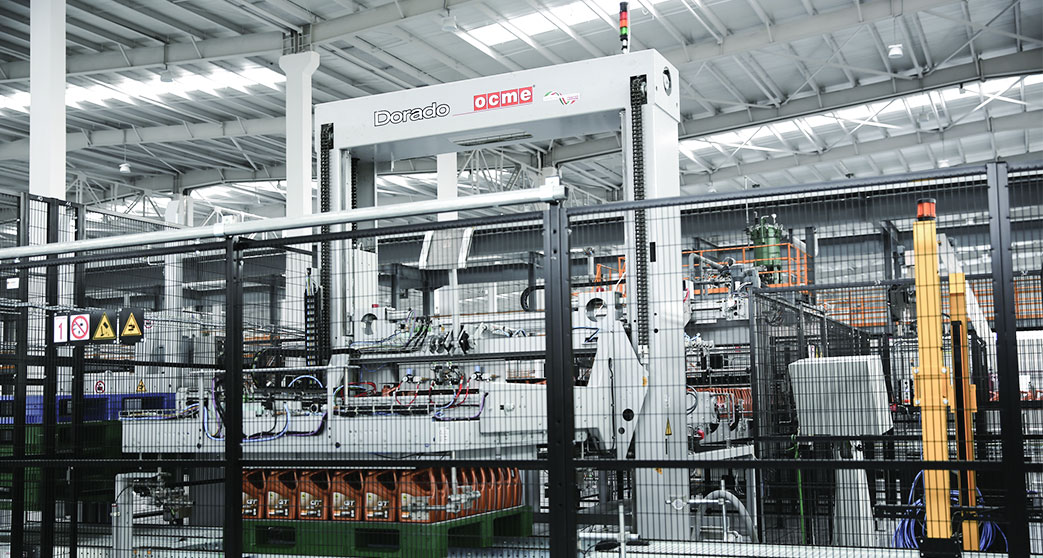
The automatic depalletising machine is composed of depalletizing area, pallet unpacking area, product output area, pallet conveyor area, pallet stacker area, product export conveyor area, sandwich extraction car area, etc. Automatic depalletising is realized through the output conveyor.
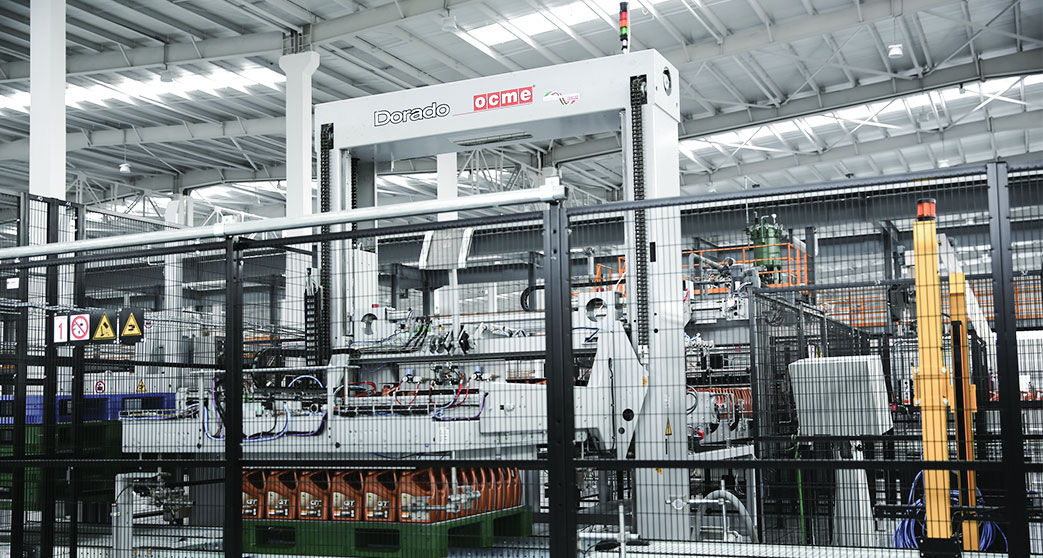
The rotary weight filler machine can achieve the actual filling speed of 9600~12000 bottles/hour for 1L products and 6000~9000 bottles/hour for 4L products, and ensure the filling accuracy within 2g.
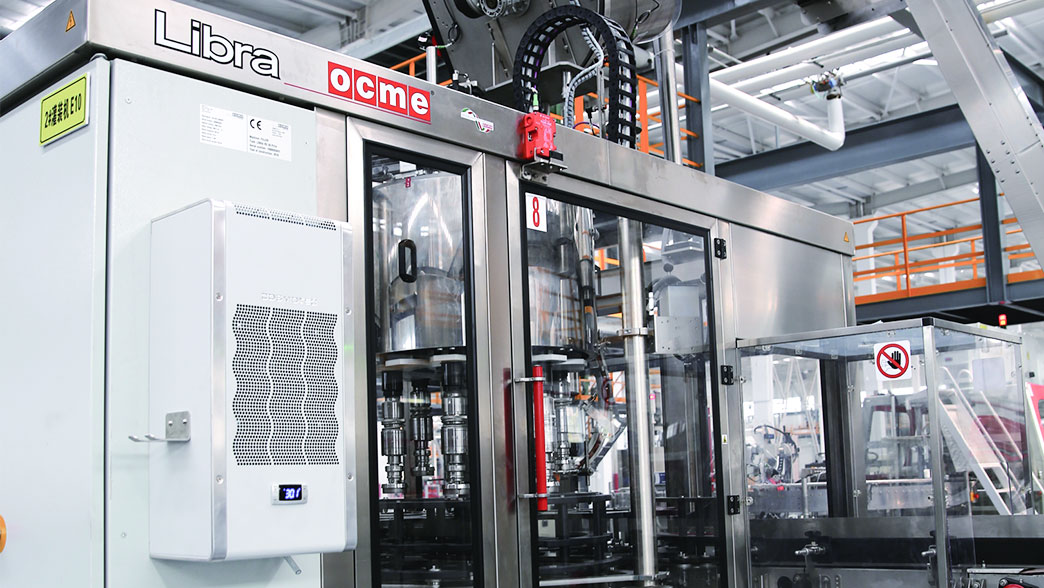
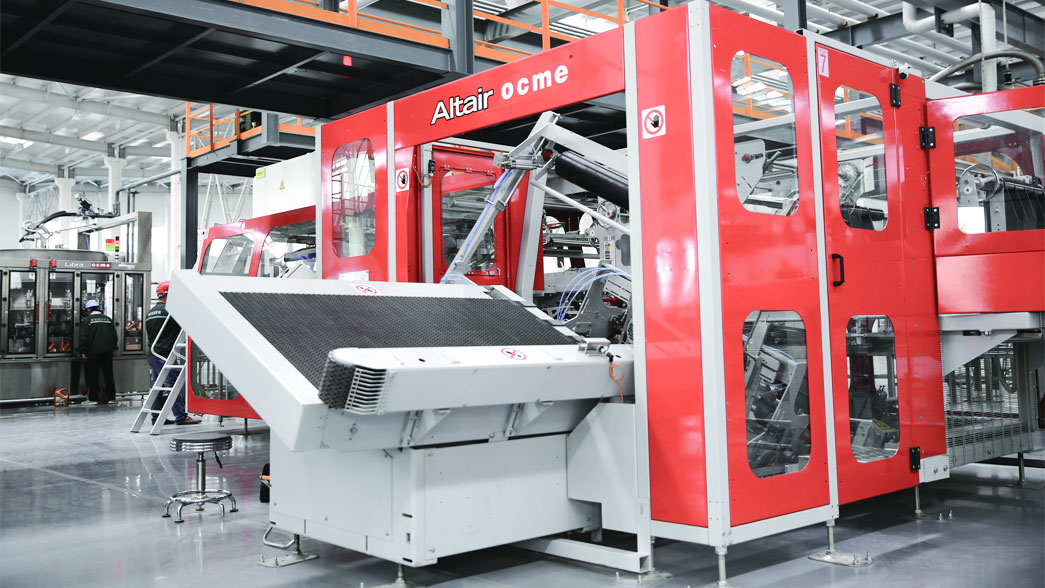
The automatic packer is a secondary packing machine developed by OCME, which focuses on high efficiency and productivity. Before packaging, the automatic lane divider will separate the products into different lanes. The cardboard library will provide the cardboard needed for packaging to automatically pack and seal the products in the whole packing machine at an average speed of 65 cases/min. It has the characteristics of convenient operation, saving glue, high efficiency and safety.
The products sealed by the automatic packer are neat and beautiful in appearance.
The sealing method of the automatic packer is gluing, which has a certain anti-counterfeiting and channeling function, clean and environmental protection.
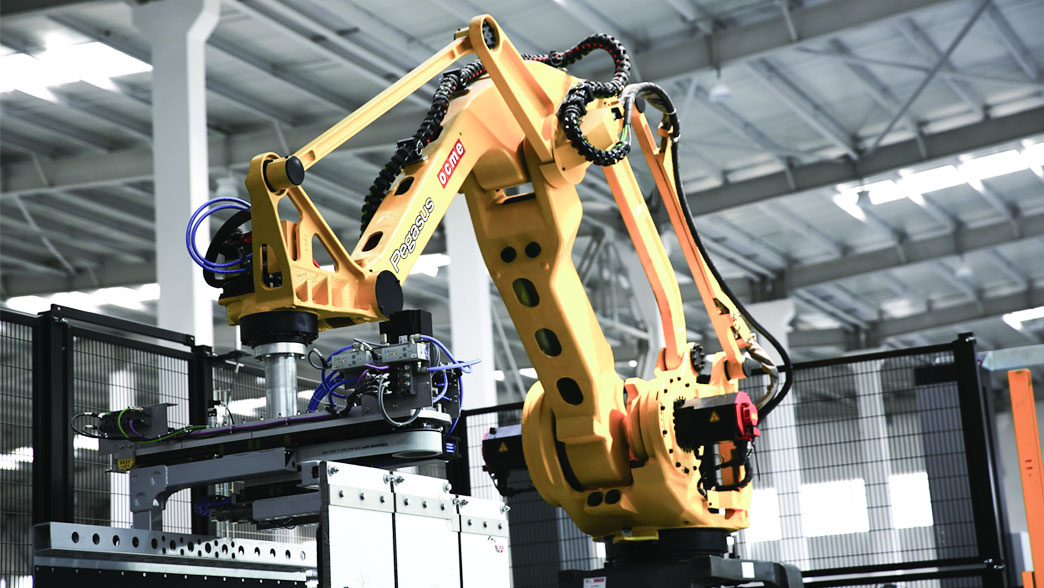
After the products are packed and sealed by the automatic packer, they are palletised by the palletiser after labeling machine and rechecking weighing machine. On the OCME automatic high-speed filler machine, the palletiser plays a final role. In the rhythm of high-speed production,the palletiser can quickly, accurately and smoothly place goods on the pallet.In addition to automatic cycling, the operator can use a handle or set parameters to operate the palletiser arm to suit the needs of production.
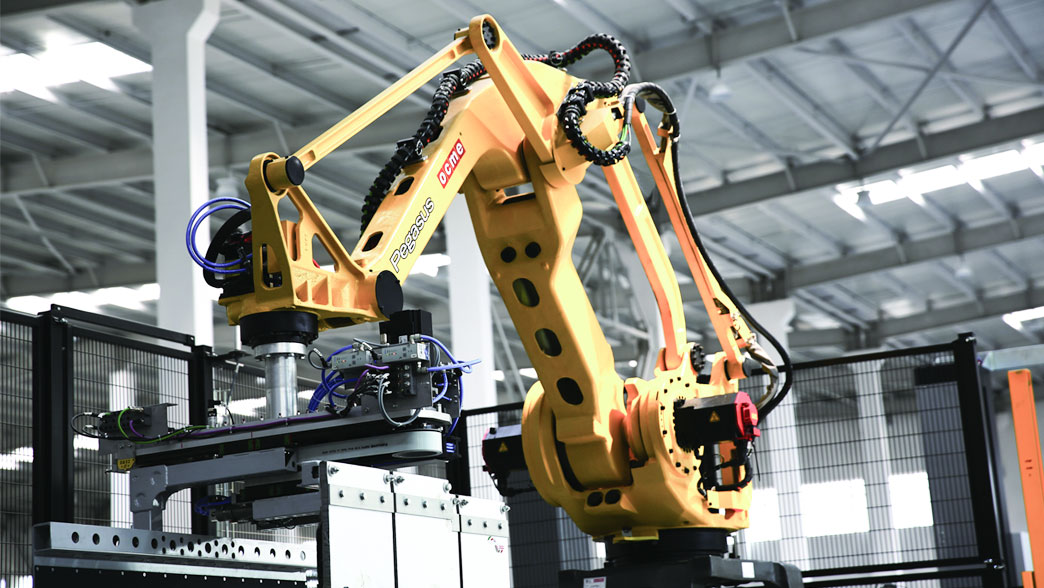
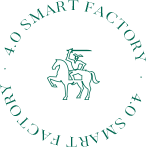
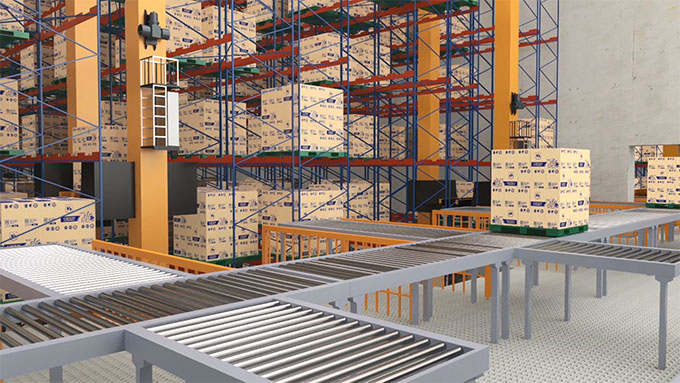
The automatic storage center is mainly composed of shelves, tunnel type stacking crane, in (out) warehouse platform, dispatching control system and management system. It implements AS/RS by the cooperation of automatic storage equipment and computer management system. The automated storage center has a total of 10,560 spaces and can accommodate 600,000 pieces of goods at the same time. The automatic storage center realizes the three-dimensional storage, automatic access and standardized management of warehouse goods, combined with warehouse management software, graphic monitoring and scheduling software, bar code identification and tracking system, cargo sorting system, stacker recognition system, stacker control system, cargo space detector and so on.
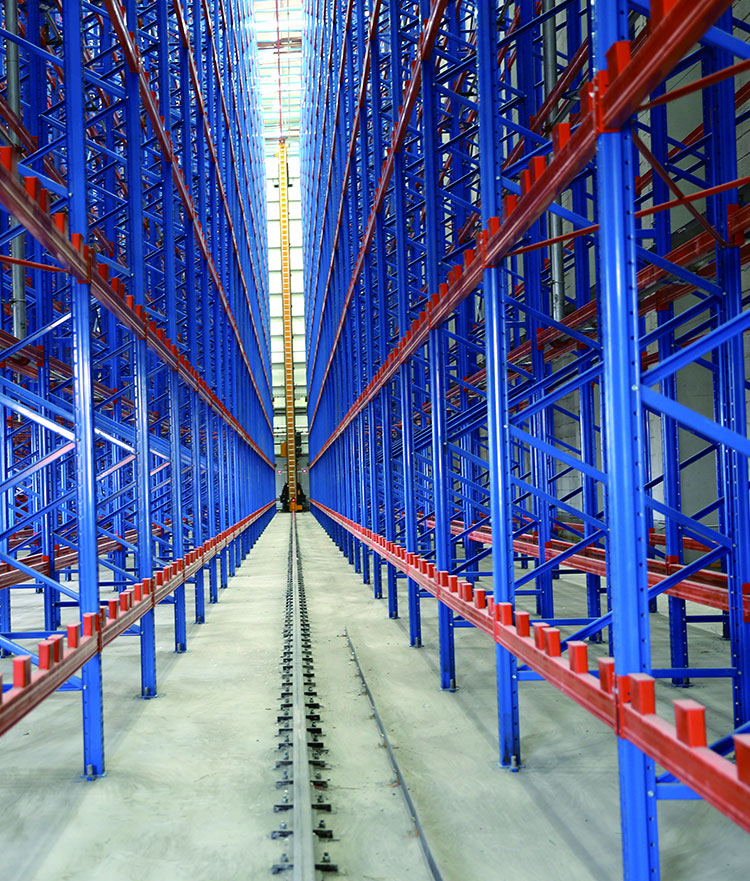